Sommaire
Dans un monde où l'innovation technologique ne cesse de repousser les limites du possible, l'industrie chimique a su évoluer pour répondre aux normes de sécurité et d'efficacité toujours plus exigeantes. Les systèmes de rétention sont au cœur de cette transformation, jouant un rôle déterminant dans la prévention des accidents et la protection de l'environnement. Cette exploration vous convie à découvrir comment l'ingénierie moderne façonne l'avenir de l'industrie chimique à travers des avancées technologiques sans précédent. De la conception innovante aux matériaux révolutionnaires, en passant par l'intégration de l'intelligence artificielle, chaque avancée ouvre un nouveau champ des possibles. Laissez-vous guider dans ce voyage au cœur des systèmes de rétention de dernière génération et saisissez l'étendue des améliorations qui transforment cette industrie essentielle. L'heure est venue de lever le voile sur les technologies qui redéfinissent les standards de sécurité et d'efficience dans l'industrie chimique.
Les nouveaux matériaux et leur impact sur la rétention
Les avancées dans le domaine des matériaux innovants ont un impact significatif sur l'efficacité des systèmes de rétention utilisés dans l'industrie chimique. L'introduction de polymères à haute performance, par exemple, a révolutionné la conception de ces systèmes en offrant une résistance chimique sans précédent. Ces matériaux se distinguent non seulement par leur capacité à résister à des produits chimiques agressifs, mais également par leur durabilité exceptionnelle, réduisant ainsi le besoin de remplacement fréquent et contribuant à la diminution de l'empreinte environnementale.
En outre, l'adhésion aux réglementations environnementales est devenue un enjeu central pour l'industrie chimique. Les nouveaux matériaux de rétention aident les entreprises à se conformer à ces normes de plus en plus strictes, tout en apportant une contribution essentielle à la réduction des risques de contamination et d'accidents environnementaux. Ce progrès technique s'inscrit donc dans une démarche de développement durable, qui bénéficie à la fois à l'environnement et à la sécurité industrielle. Pour en savoir plus sur l'importance des bacs de rétention dans l'industrie chimique et découvrir l'apport de ces matériaux innovants, cliquez pour accéder à la page.
L'avènement de l'automatisation et de la surveillance intelligente
L'intégration de l'automatisation et de la surveillance intelligente marque un tournant significatif dans la gestion des risques au sein des installations chimiques. Ces systèmes novateurs, qui allient capteurs de haute précision et intelligence artificielle (IA), offrent une capacité inégalée à surveiller en continu l'intégrité structurelle et le bon fonctionnement des équipements. La mise en oeuvre d'un système de détection des fuites sophistiqué permet d'identifier les anomalies qui pourraient signaler une défaillance imminente. De façon préventive, l'analyse des données recueillies par l'IA conduit à des interventions de maintenance prédictive, réduisant ainsi les périodes d'arrêt non planifiées et prolongeant la durée de vie des composants critiques. Cette avancée technologique assure une protection accrue contre les incidents, tout en optimisant les ressources et la sécurité globale des opérations industrielles.
La conception modulaire des systèmes de rétention
La conception modulaire des systèmes de rétention représente une avancée significative dans l'industrie chimique. Ces dispositifs innovants, tels que la cuve de rétention modulaire, offrent une flexibilité inégalée, permettant une adaptation sur mesure aux contraintes spécifiques de chaque site de production chimique. En effet, l'installation facile des éléments modulaires accélère considérablement la mise en place des systèmes de rétention, réduisant ainsi les temps d'arrêt et optimisant la continuité des opérations industrielles.
L'adaptabilité est un autre avantage clé de ces systèmes. Ils peuvent être aisément reconfigurés ou étendus en fonction de l'évolution des besoins de production ou des réglementations environnementales. De surcroît, la nature modulaire de ces systèmes facilite grandement leur transport, leur permettant d'être déplacés ou réutilisés en différents points d'un même site ou entre plusieurs sites, assurant ainsi une gestion optimale de la sécurité et de l'efficacité dans l'industrie chimique.
L'intégration des normes internationales
La mise en conformité avec les normes internationales est un aspect déterminant dans la conception des systèmes de rétention pour l'industrie chimique. L'adoption de standards tels que l'ISO 14001 joue un rôle prépondérant dans l'assurance de la compatibilité globale et de la sécurité des systèmes. En effet, ces réglementations établissent des exigences précises en matière d'environnement et de gestion des risques, facilitant ainsi l'interopérabilité des technologies à travers les différentes régions du monde.
L'harmonisation des pratiques selon les normes internationales engendre des avantages significatifs en termes de compétitivité. Les entreprises qui intègrent ces standards dans leurs processus attestent de leur engagement en faveur de la qualité et de la sécurité, éléments fondamentaux pour se démarquer sur le marché international. Par ailleurs, cette conformité est souvent perçue comme un gage de fiabilité par les clients et peut conduire à une meilleure pénétration de marché ainsi qu'à l'ouverture de nouvelles opportunités commerciales.
Le rôle de l'économie circulaire dans l'évolution des systèmes de rétention
Confrontée aux enjeux environnementaux, l'industrie chimique intègre désormais les principes de l'économie circulaire dans la conception des systèmes de rétention. L'écoconception, terme technique désignant une approche visant à minimiser l'impact écologique dès la phase de design, devient une pratique de premier plan. Grâce à elle, la réutilisation et le recyclage des matériaux constituent la pierre angulaire des nouveaux dispositifs.
La minimisation des déchets est également au cœur des préoccupations. Les systèmes de rétention sont conçus pour garantir une durée de vie prolongée et une fin de vie responsable, où les composants peuvent être facilement démontés et intégrés dans de nouveaux cycles de production. L'optimisation des ressources passe par l'utilisation de matériaux recyclés et la réduction de la consommation de matières premières neuves, contribuant ainsi à la réduction de l'empreinte carbone de l'industrie.
Similaire

Comment ChatGPT en français révolutionne l'apprentissage des langues ?
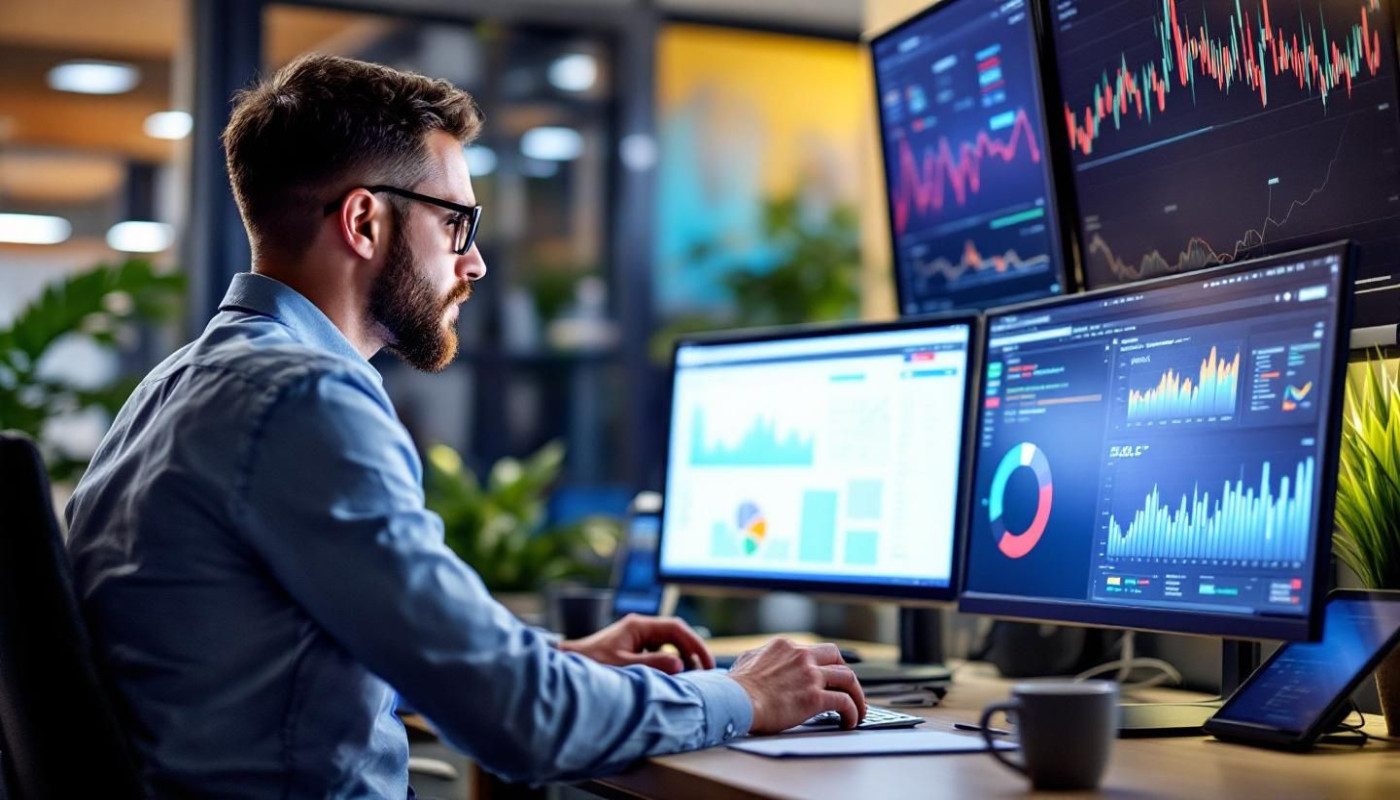
Comment un consultant SEO peut transformer votre présence en ligne
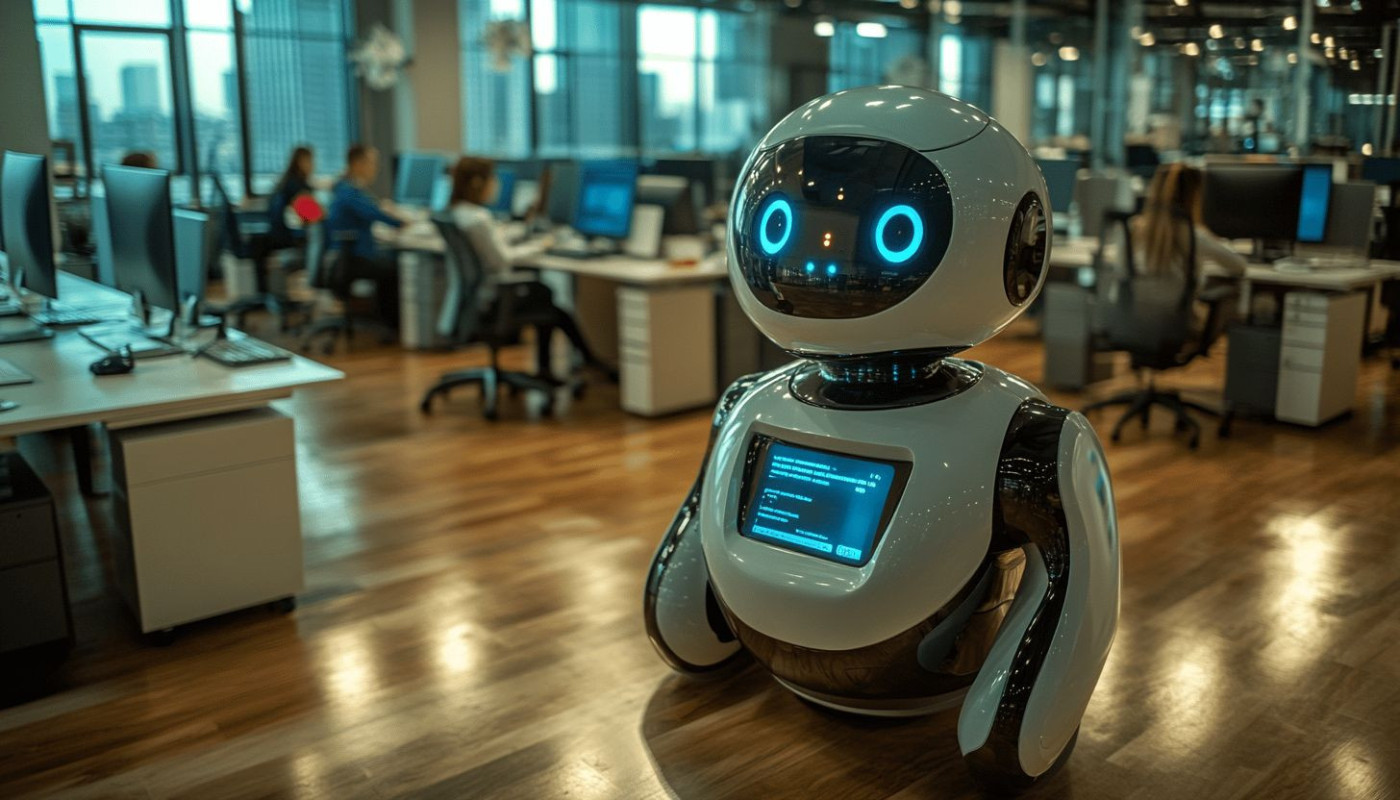
Comment les chatbots IA transforment-ils le service client ?
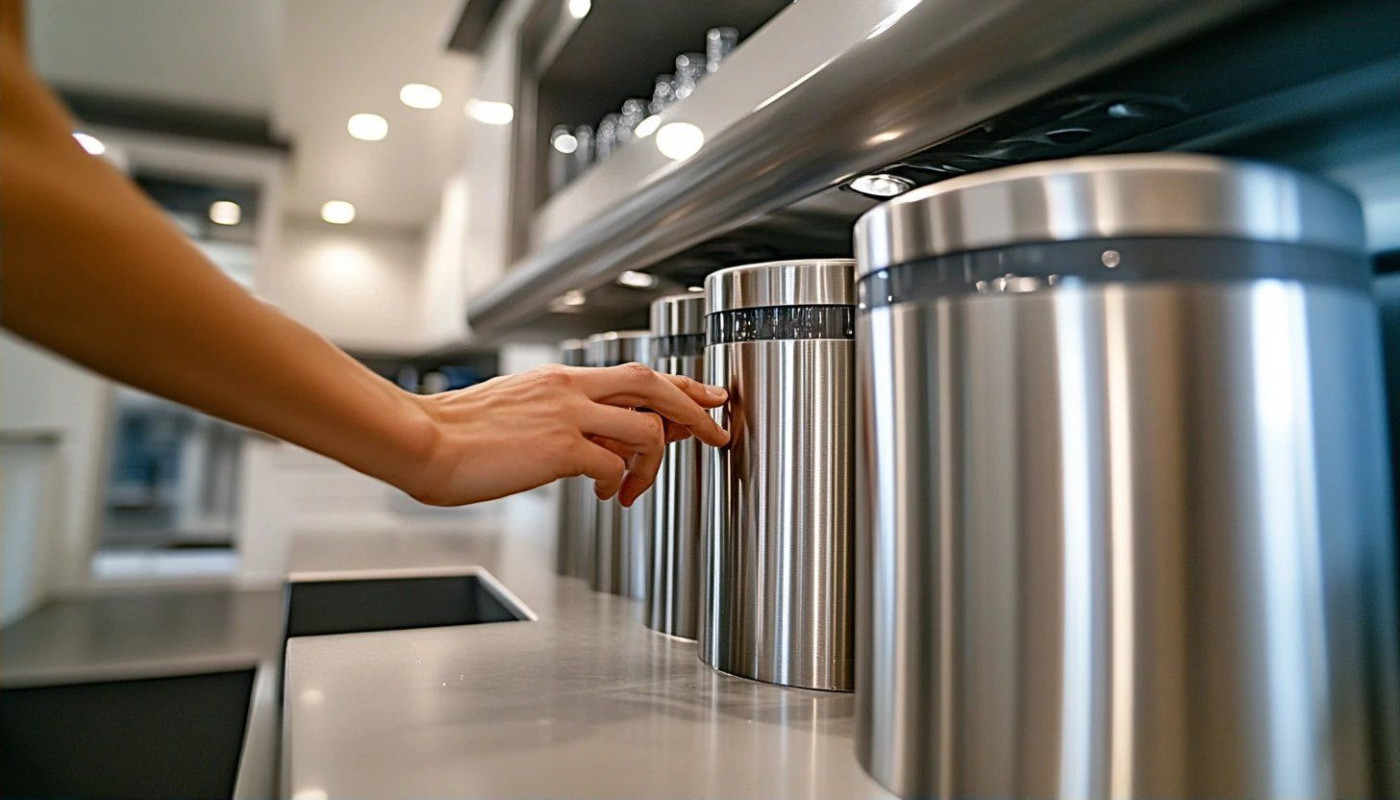
Comment l'installation d'un système de filtration peut transformer votre quotidien ?
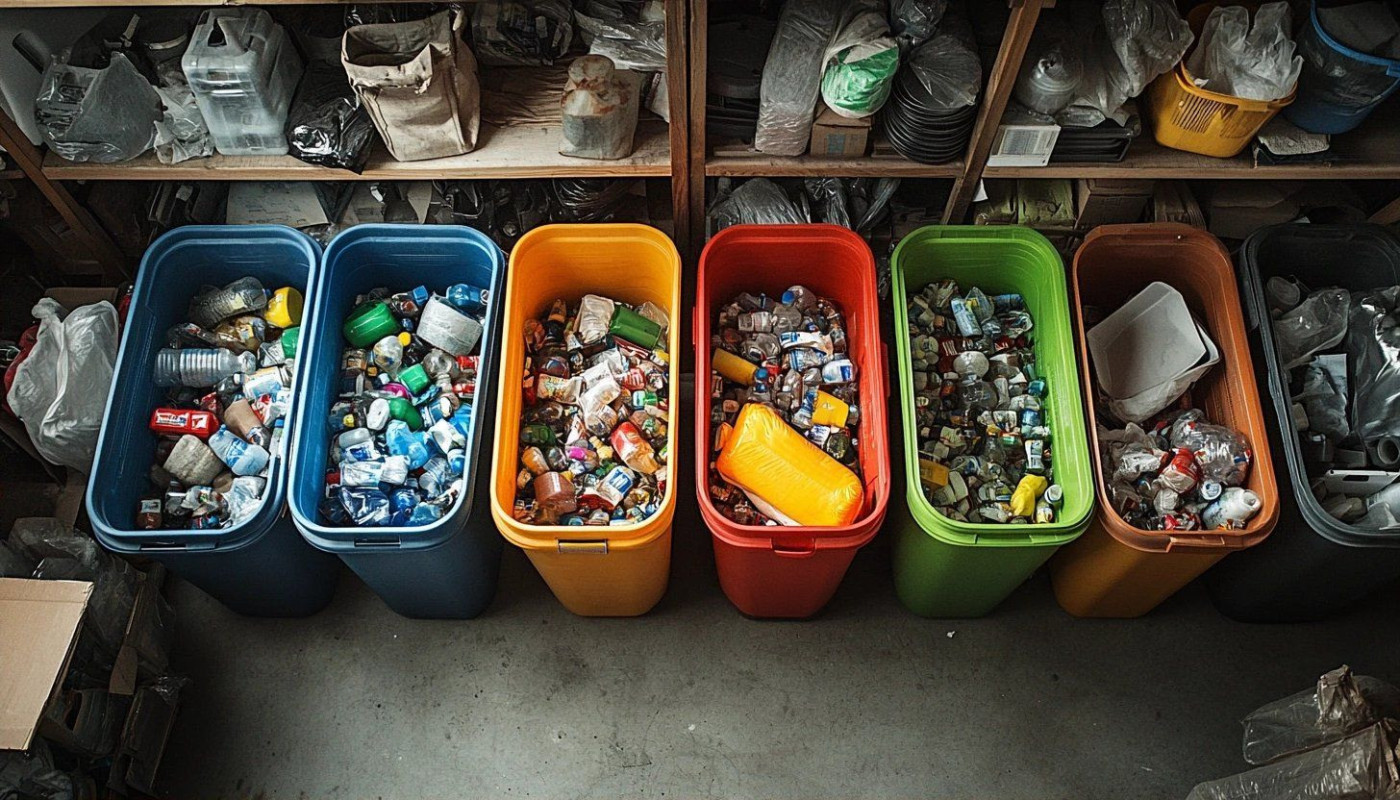
Comment optimiser le recyclage lors du débarras d'espaces ?

Blockchain et secteur public applications potentielles pour une transparence accrue

Comment choisir une plateforme fiable pour des rencontres en ligne en 2025

Démystifier la 5G avantages et défis pour les utilisateurs en 2023

Optimisation de l'espace pour composteurs dans les petits appartements
